DESIGNED
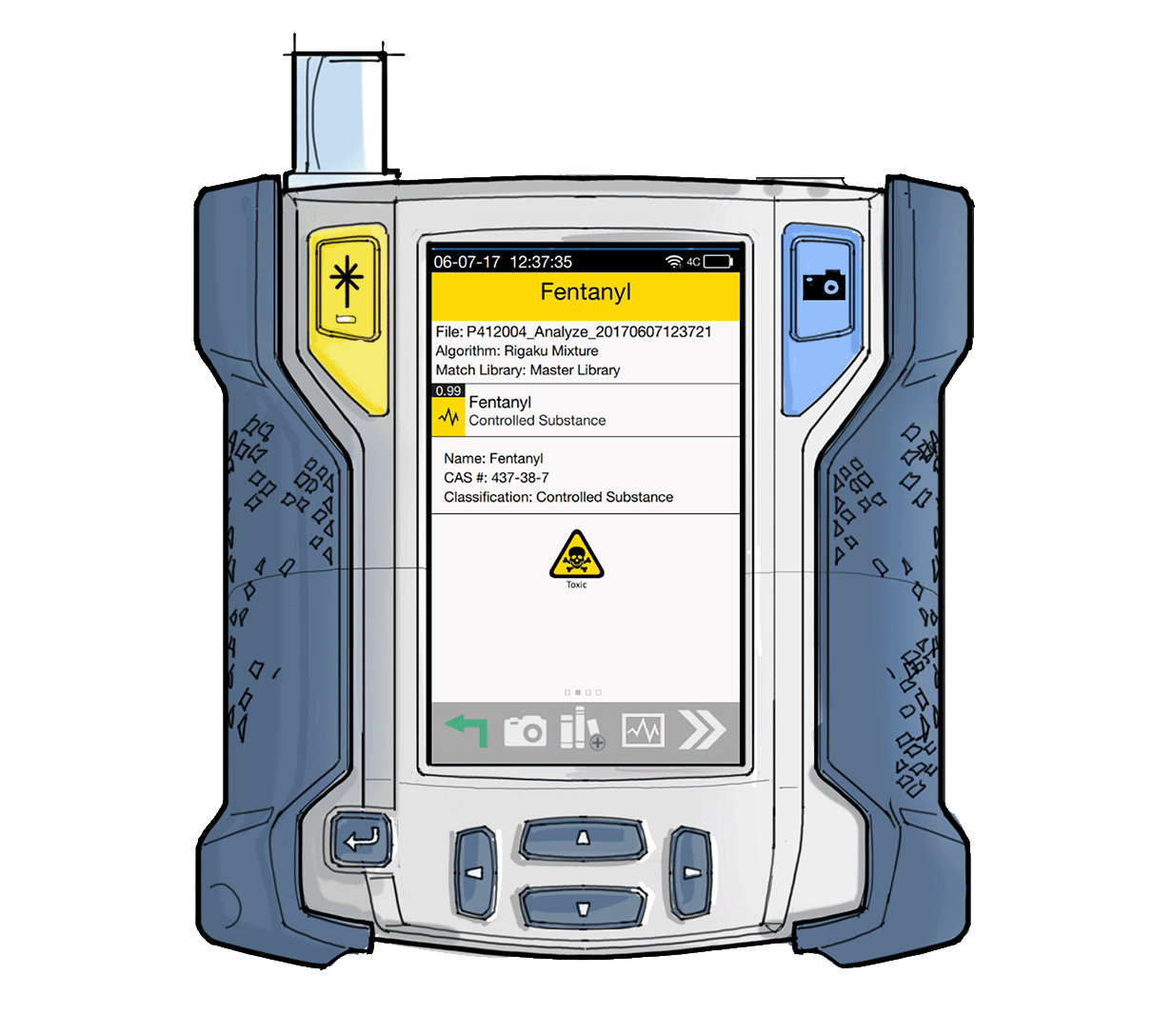
TESTED
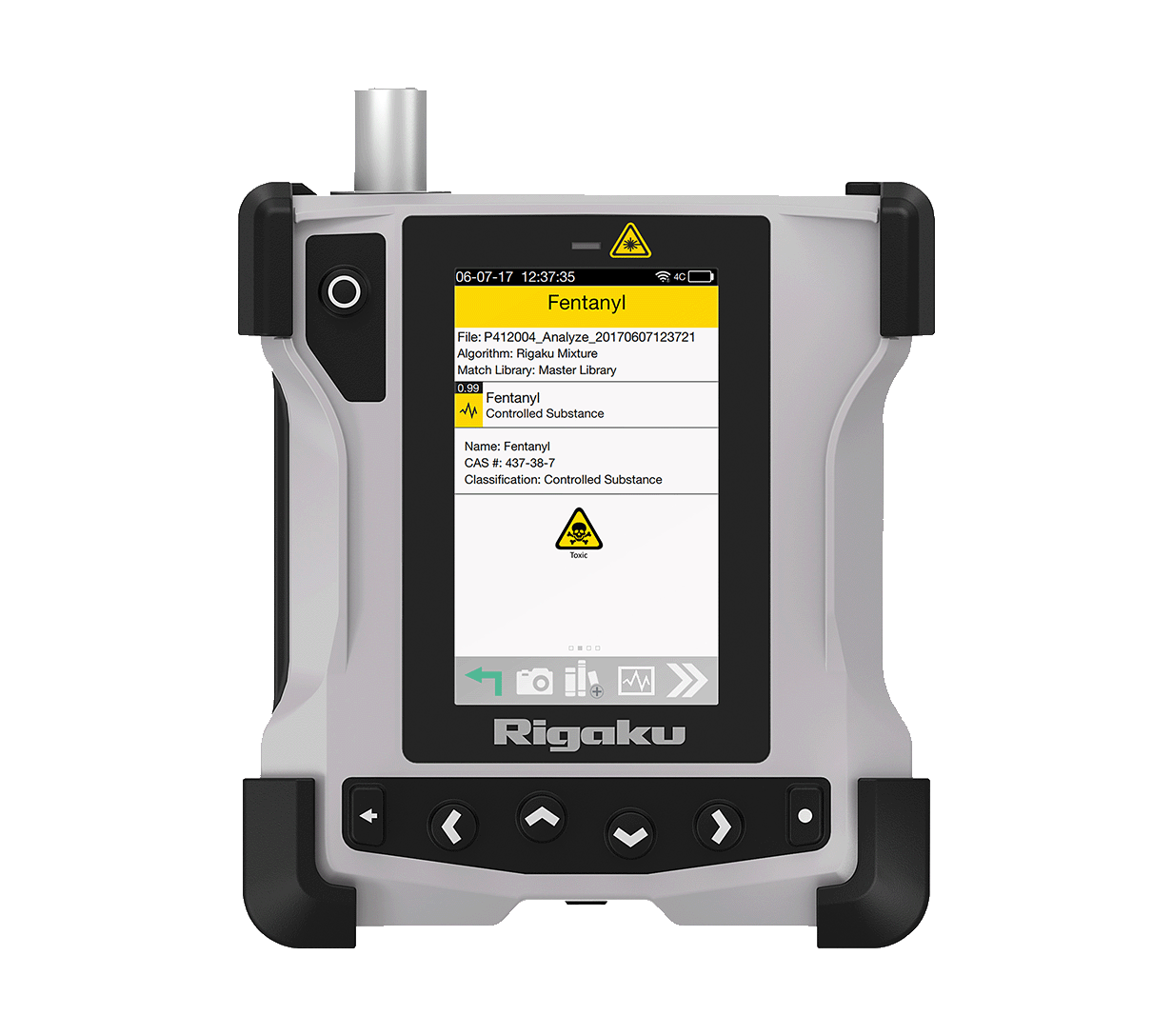
PRODUCED
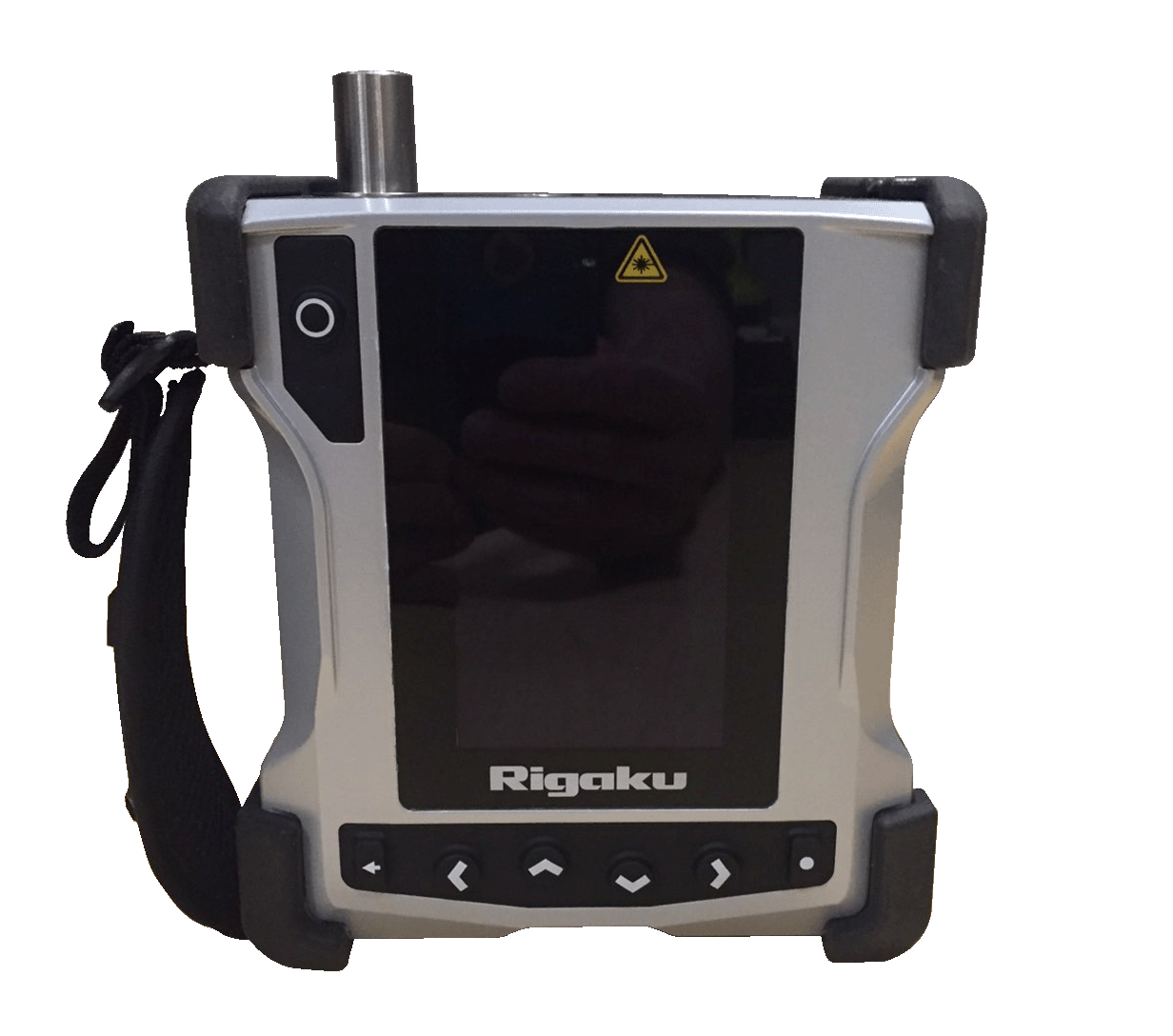
LEAVE NOTHING TO CHANCE
You haven’t invested all your time, energy and money to get this far only to have your product fail in the field. You need a partner with experience in the design and engineering of tactical, mobile equipment. From a deep understanding of the user and getting the ergonomics correct to exceeding MIL-STD testing for drop protection, sealing and EMI shielding, Juggernaut.Case guides the way.
We have worked with hundreds of government agencies and private companies to design heavy-duty phone cases, mounts and cables that let the end user focus on the mission. This could be as simple as adapting one of our tactical device cases to fit a certain phone model or modifying a charging cable to fit a different connection port. We can also come up with special vehicle mounts, body mounts, charging solutions and other rugged products to accommodate unique field op neeeds while integrating with the exisiting Juggernaut.Case lineup.
||
DESIGN SERVICES
Rugged product design that is designed, tested and produced for you.
Designing products for tactical applications requires specific expertise that many development teams don’t have. Since 2000, Juggernaut has advanced as a leader in the industrial design and mechanical engineering of products that are used in extreme environments. With our proven process, you can avoid costly U-turns, reduce costs and increase the speed from the drafting board to the field. If your product specifications require drop protection, environmental sealing, or specialized integration, we can help.
Note: each project requires a certain minimum order to account for development, engineering, tooling and testing costs. This minimum will vary depending on the project. Schedule a call for a free assessment of whether Juggernaut.Case may be a fit for your project.
SCHEDULE A CALL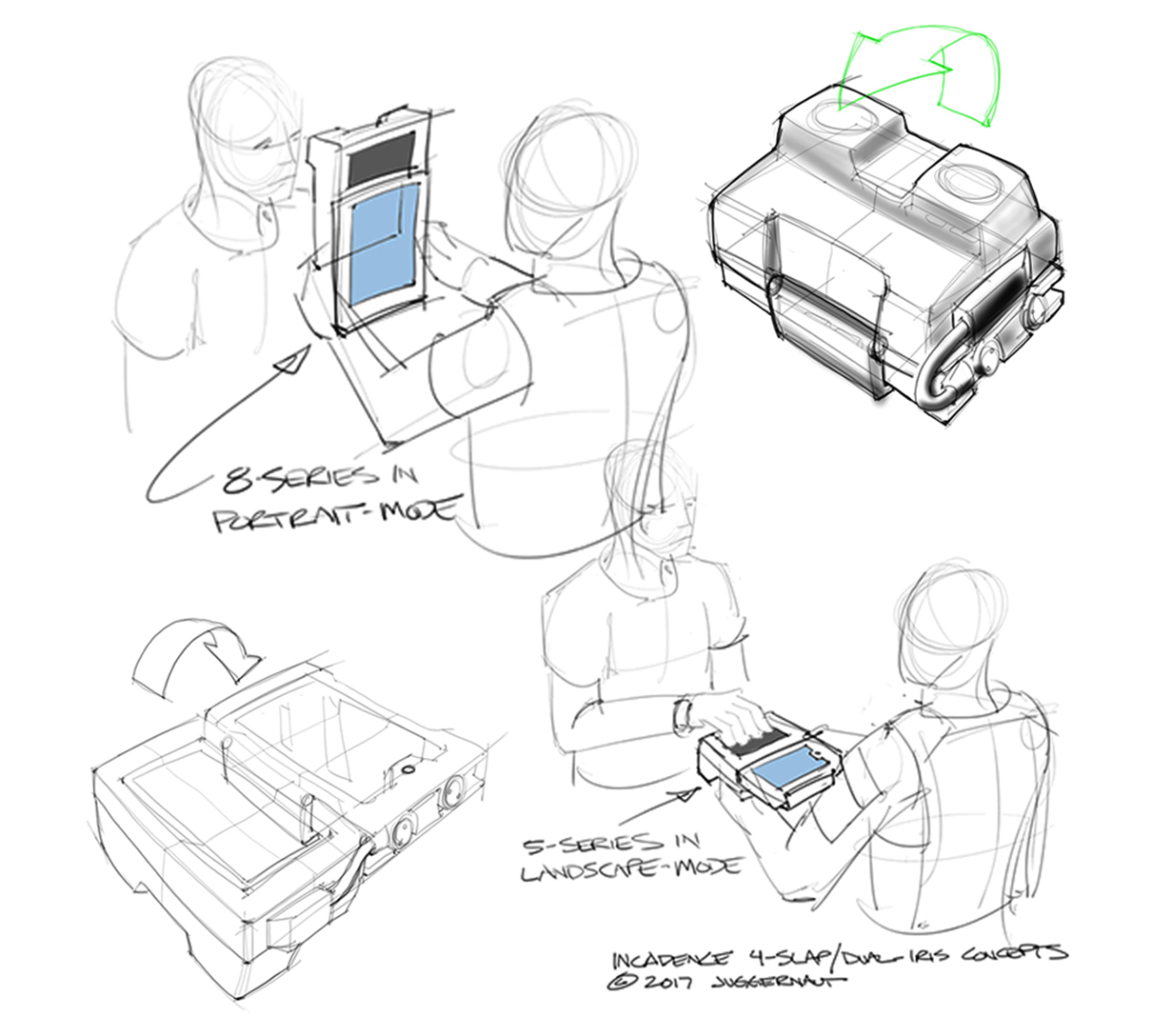
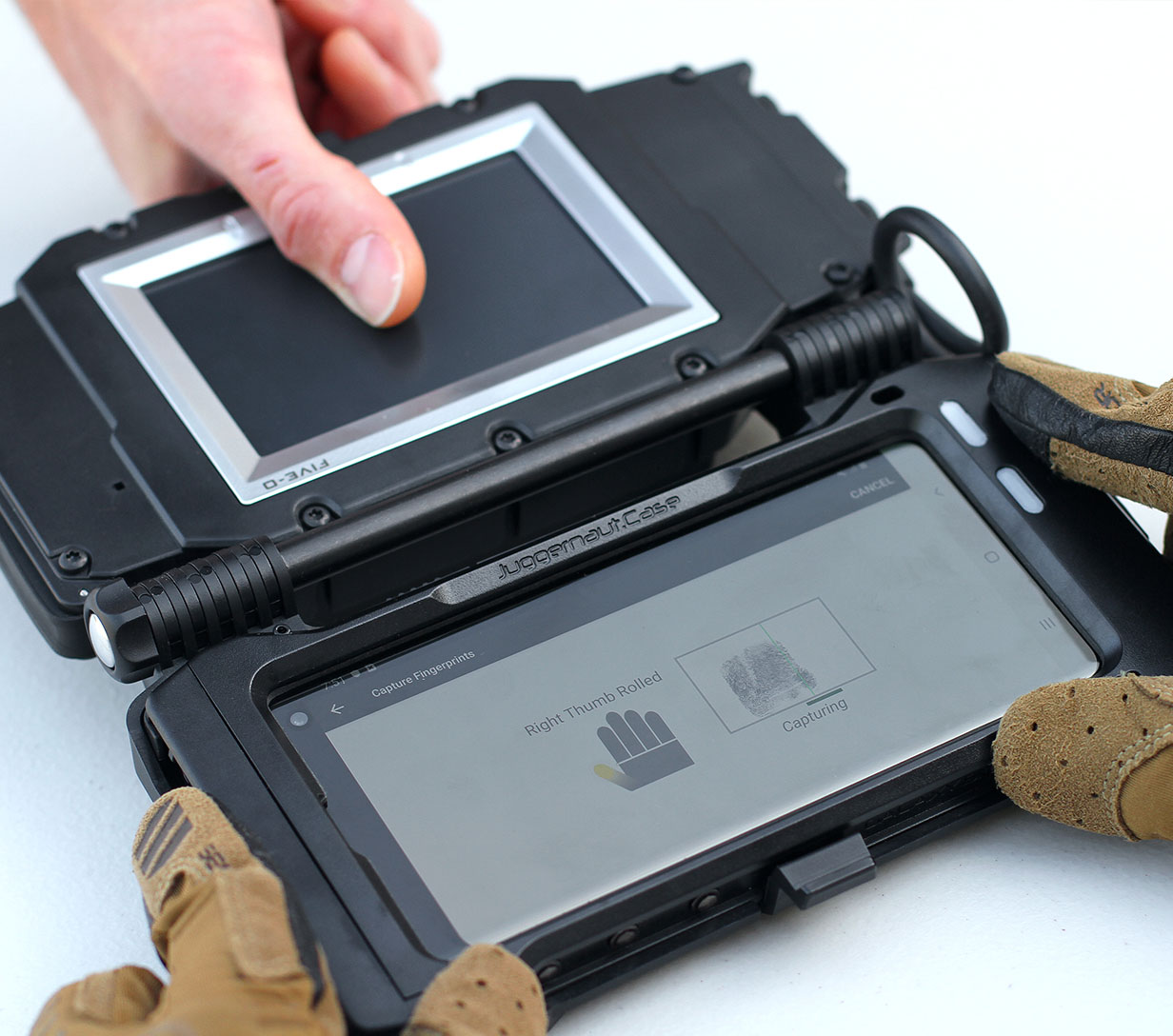
INTEGRATION
Explore the possibilities!
Leverage the Juggernaut.Case ecosystem of products to speed the path for your technology to the field. See what protect, mount and connect products we currently sell, and which ones align closest with your goals.
- System EUD
- Wearable mounting
- Vehicle mounting
- Rugged enclosures
- Sealed connectivity
- Custom cables
HEAR IT FROM OUR PARTNERS
John McIntyre Vice President, Biometrics and Identity Xator Corporation
"We teamed with Juggernaut.Case to design, test and manufacture our line of field biometric devices. We were able to leverage their standard EUD cases and cables to create an efficient and rapid development path. Juggernaut.Case understands the demands of the tactical operator and ensured that our products will be successful in the field."
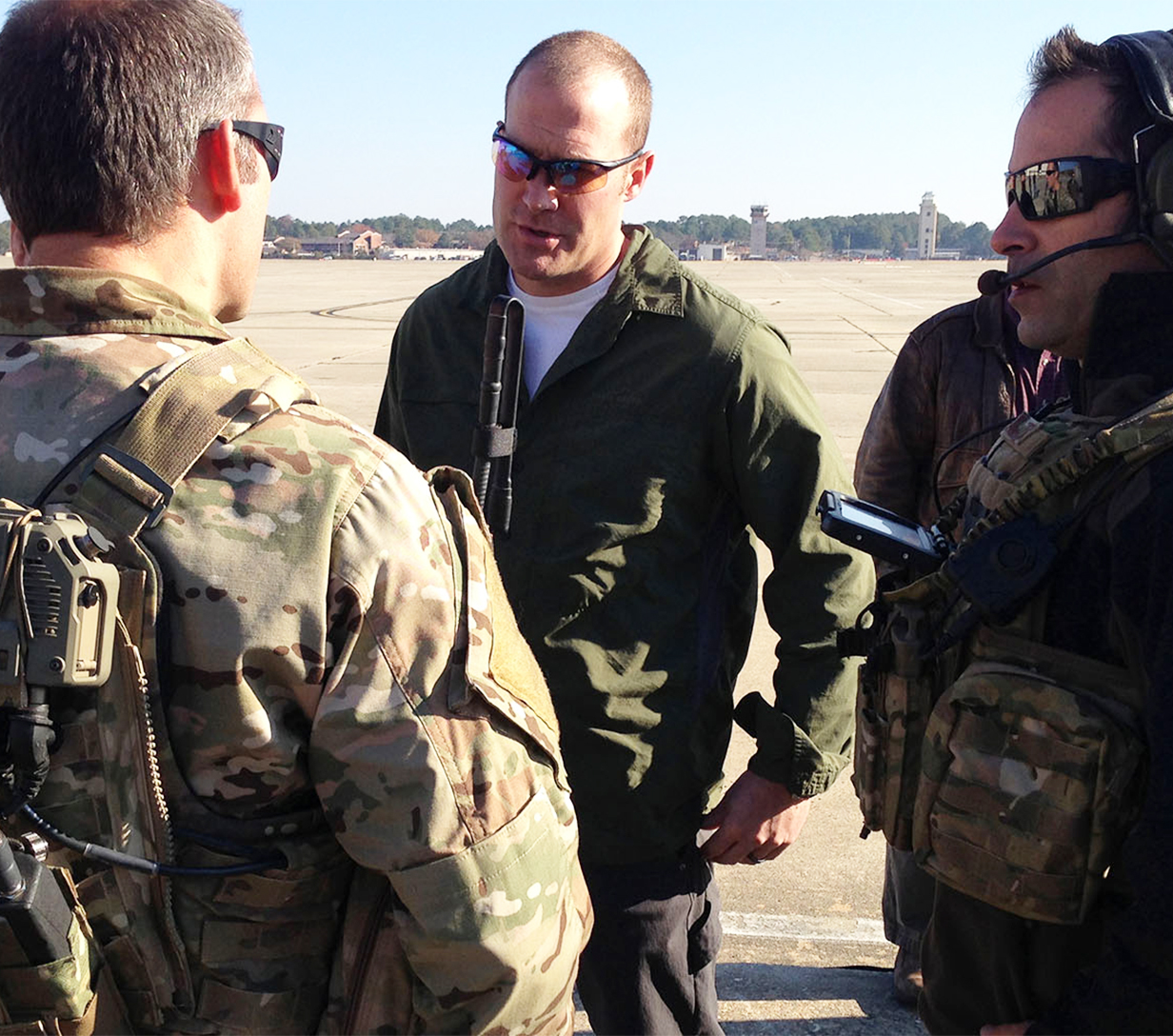
RUGGED EXPERIENCE
We have over 20 years of experience focused on the development of rugged solutions to make sure your project passes the test.
SPEED TO FIELD
Our proven process and the option to leverage our ecosystem of standard COTS product provide a fast track to the field.
TURNKEY PRODUCTION
Our in-house production and testing team combine with a proven supply chain to provide a complete solution.